Article: Advantagemedia.com
Conclusion reached after inspection with sensor film
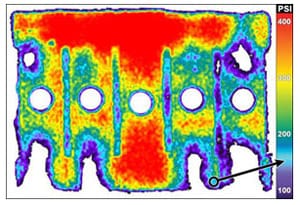
The clamping pressure used to bond Futek’s metal foil strain gauge to the tranducer body was not initially uniform, as verified by Pressurex® film.
Futek. a U.S. manufacturer and supplier of load cells, torque and pressure sensors, recently experienced difficulty assembling some of its load cells to specifications. By performing several tests, and controlling different variables, the company found fluctuations in clamping pressure to be a significant factor.
For the tests, the company used Pressurex®, a thin flexible film from Sensor Products, which is a versatile NDT tool for quality control and machine component inspection. The film has the ability to show inconsistencies in surface pressure between mating or contacting surfaces and has lowered scrap rate and assisted in the design and manufacture of many industrial and electronic products.
Futek’s sensors incorporate metal foil strain gauge technology. The adhesive they use to bond the gauges to their sensors requires a clamping pressure of 50 to 75 psi. James Meiselbach. a mechanical engineer at Futek, used the thin film to see that the clamping pressure fluctuated from 50 psi to upwards of 200 psi in some of the production runs.
This discovery led Futek to redesign several of its clamps to incorporate silicone die springs to regulate the pressure more precisely. "A sample pack of Pressurex®with film that revealed different surface pressure ranges allowed our production to continue, says Meiselbach.
Meiselbach found Pressurex® to be simple to work with. To measure the surface pressure of a clamp around the outside of a load cell, he cut the film in the configuration of the clamp surface area, placed it in between the clamp and the load cell, applied force and unclamped it, He compared the film, which changed color depending on how much pressure is exerted, to an accompanying color calibration chart.
The Film reveals surface pressure from 2 to 43,200 psi (0.14 to 3,000 kg/cm²) No training is required and the film can assess surface contact inconsistencies in virtually and industrial or electronic application, including gaskets, clamps, bolted joints, connectors, heat sinks, heat sealing elements and welding heads.
Meiselbach first became aware of the product when he previously worked for an aerospace company. ‘We were having a problem with the main rotor blade of a helicopter. Interference was causing a fatigue crack in one of the inner spar tubes of the rotor blade,’ Meiselbach recalls. ‘We put a large sheet of Pressurex in the bonding tool, bagged it up, and pressurized it in the autoclave. When we removed the film, we were able to identify the exact amount of pressure causing the crack.’
Sensor Products Offers More On Fastening Technology & Bolted Joint Design
Seminars For Engineers is offering the Fastening Technology & Bolted Joint Design Sem/ttarfrom May 23-29, 2003 in Los Angeles, CA.
The two-day seminar was developed to give engineers and other technical personnel current specifications for, and a better understanding of the complexities of mechanical jointing with fasteners.
Insufficient guidelines and outdated information are not adequately equipping engineers for real life design challenges. This can lead to catastrophicfailures or costly over-designs. The Federal regulations (Fastener Quality Act) on these often safety critical design elements have caused a renewed focus on the proper use of fasteners.
The seminar incorporates the most recent techniques and guidelines from both international and domestic engineering societies and research groups and provides attendees with immediately applicable knowledge. According to the company, attendees will:
- Gain understanding of the bolted/screwed joint and elastic interactions.
- Learn how to determine preload stresses.
- Select proper tightening methods.
- Evaluate dissimilar materials for thermal expansion and galvanic properties.
- Understand loosening causalities.
- Learn the optimal design for fasteners.
- Calculate safety factors and limitations.