Composites are engineered materials composed of a matrix material (e.g. polyester or epoxy resins) and a reinforcing material (e.g. glass mat or woven fabric). The process of making a composite is termed Composite Layup, which is derived from the original method of making these materials.
In hand layup (see Figure 1) the resins are impregnated by hand into the reinforcing fibers. Rollers and brushes are used to incorporate the resin into the fibers and to remove air from the composite.
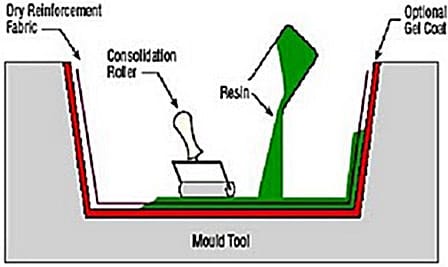
Fig 1: Hand Layup of Composite Material
Hand layup is a low volume, labor intensive method suited for boat hulls or other large items. The fibers are positioned manually in the open mold, and resin is poured, brushed, or sprayed over the mat. Room temperature curing resins are commonly used. For a high quality part surface, a pigmented gel coat is first applied to the mold surface.
A variety of molding methods can be used according to the end-item design. The matrix and reinforcement materials are important factors as is the quantity to be produced. Large quantities often justify expenditures for automated equipment. Some of the manufacturing methods are vacuum bag molding, pressure bag molding, autoclave molding or Resin Transfer Molding (RTM).
A common manufacturing method is to use reinforcements that are pre-impregnated with resin. Such reinforcements are called prepreg. Prepreg is usually stored in cooled areas since activation is most commonly done by heat during composite molding. Prepreg technology is used to lower cost and enhance performance of the completed composites. The resin matrix is applied to the reinforcement, and the wetted fibers are run through nip rollers to produce the prepreg.
Control of process pressure is critical to maintaining product quality during prepreg production and composite molding operations. Fujifilm Prescale® pressure indicating film has been successfully used to obtain such pressure control. Figure 2 demonstrates the use of Fujifilm Prescale® for prepreg manufacture.
When placed in the nip rollers or platens of a prepreg laminating press, Fujifilm Prescale® instantaneously and permanently changes color in direct proportion to the pressure being applied. Conceptually similar to Litmus paper, the color Fujifilm Prescale® turns reveals the precise pressure level. It helps to achieve the following:
- Properly align rollers to ensure uniform resin application and fabric wet-out
- Detect and correct prepreg uniformity issues to reduce off-spec fiber content
- Prevent defects such as resin content inconsistency in the resin metering stage

Fig 2: Fujifilm Prescale® Film Placed between Nip Rollers
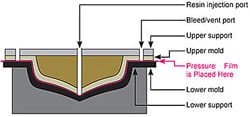
Fig 3: Fujifilm Prescale® Pressure Indicating Sensor Film for RTM Process
For RTM composites, Fujifilm Prescale® is used as a quality control method to correct and prevent defects that result if the preform does not uniformly fill the mold. As shown in Figure 3, the film is used to test the preform before the resin is injected. When uniform pressure in the mold is achieved, the results are uniform resin flow and good composite parts.
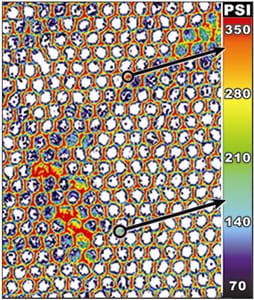
Fig 4: Topaq® Results
When using Fujifilm Prescale®, additional graphical and statistical data can be retrieved from the film through Topaq®, an optical analysis system that instantly generates full-color pressure maps and accompanying statistical data. Figure 4 shows the results of a Topaq® analysis where color variations expose inconsistencies in composite layup contact pressure.
In the aerospace industry, Fujifilm Prescale® has been used to determine the exact amount of pressure causing cracks in the inner spars of a helicopter’s main rotor blade. A large sheet of Fujifilm Prescale® was inserted into the bonding tool, bagged up, and pressurized in an autoclave. When the film was removed, the exact amount of pressure causing the crack was determined.
These are only a few examples of the benefits of Fujifilm Prescale® in composite layup manufacturing operations.