D. Spicer1, K. Lai1, K. Kornelsen1, A. Brennan1, N. Belov2, M. Wang2, T-K. Chou3, J. Heck3, T. Zhu2, S. Akhlaghi1
1Micralyne Inc.,
1911 94th Street
Edmonton, Alberta, Canada,
T6N, 1E6
[email protected]
2Nanochip Inc.,
48041 Fremont Blvd.,
Fremont, California, USA,
94538
3Intel Corporation,
2200 Mission Blvd, Santa
Clara, California, USA,
95054
ABSTRACT
Pressure non-uniformity in a wafer to wafer bond chamber was characterized using pressure sensitive paper. The effect of poor pressure uniformity is discussed, and the nonuniformity was corrected for use in a eutectic Au/Sn based wafer-to-wafer bond. Several types of under solder metallization were also investigated, with Nb/Au seed metal providing the best overall result with good solder compression, liquid proof seal, and minimal solder spill-out. Thirdly, solder compression versus pressure applied was studied to achieve an excellent gap control (2 – 3 μm) between the bonded substrates.
Keywords: AuSn solder, eutectic wafer bonding, pressure distribution, pressure paper
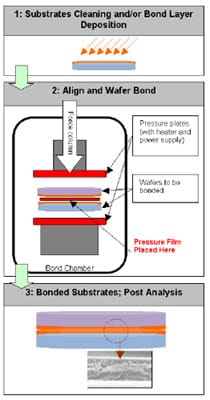
Fig. 1: Wafer Bonding Process Illustration
INTRODUCTION
Wafer to wafer bonding has become an enabling semiconductor technology in industries such as 3D packaging, MEMS, MOEMS, and SOI. In a typical wafer bonding process, two flat substrates are permanently joined (bonded) to one another by applying physical pressure, temperature, and/or electric field (see Fig. 1). Each of the above factors is set depending on the substrate materials being bonded, and the control of these parameters is crucial to a successful, high-quality, high-uniformity manufacturing process.
Of the above three major parameters in a bond recipe, electric field and temperature are readily measurable within a wafer bonding chamber using built-in electronics and thermocouples. Pressure, on the other hand, is usually measured in the tool as the total amount of force exerted over the pressure column. This measured force is then used to calculate the average pressure, assuming perfectly flat pressure plates. In practice, the pressure plates are often non-ideal, or they may have degraded over time. This leads to potential pressure variations that are not detected by the control software. Poor distribution of pressure can lead to poorly bonded or completely unbonded wafer areas, cracked wafers, or premature wear of the pressure plates.
The significance of a uniform applied pressure in a bonding process depends largely on the specific materials being bonded. For example, in an anodic bonding process, silicon is bonded to glass by applying a large electric field (e.g. 500V) at elevated temperatures (e.g. > 300 °C) [1]. The reaction between silicon and oxygen then forms a very strong SiO2 bond. Because the magnitude of the electrostatic forces is generally sufficient for a full bond, physical applied pressure is neither critical nor required for this type of bond process.
On the other hand, the control of applied pressure is important in eutectic or thermocompression bonding processes, where two arbitrary substrates are bonded together using thin intermediate films that are often metallic alloys (Ref. 1-3). In this type of bond, the two surfaces to be bonded are brought in contact and temperature is increased to above the eutectic point. Once the eutectic temperature is reached, the solder liquefies and wafers bond if they are in contact. High pressure can cause the liquefied solder to physically compress and potentially spread onto unwanted regions and cause short circuits. Too little pressure would typically result in weakly bonded or completely unbonded regions. And in practice, for a nonoptimized bonding system (considering bond process parameters as well as materials used), both spill outs and unbonded regions can be found on the same pair of substrates due to pressure, temperature, or solder nonuniformities. Therefore, the characterization of applied pressure measured directly at the substrate is an important aspect in the development of a high yielding bond processes.
1: Pressure Indicating Film Experiment
Pressurex® film is a pressure sensitive film that measures pressure from 2 – 43,200 psi (0.14 – 3,000 kg/cm2). When placed between contacting surfaces it permanently changes color proportionally with the pressure applied. Absolute pressure magnitudes were calibrated using known pressures, which were then used to analyse scanned pressure maps and create coloured pressure maps such as that shown in Fig. 2b.
By running a bond recipe with the pressure set to 4 bar, a direct imprint is formed on an appropriate grade of pressure film. Figure 2a shows an image film taken from a 6″ diameter bonding tool with poor pressure uniformity. The colour map in 2b emphasizes the donut shaped high pressure ring, and the line scan in Fig. 2c shows outer ring pressures exceeding 15 bar and less than 3 bar at the center.
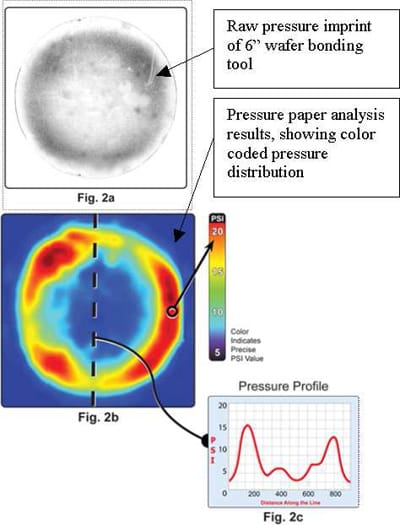
Fig. 2: Bond tool images showing pressure inconsistencies.
A series of adjustments to the pressure column of the bond tool were then made, and the pressure uniformity was evaluated by running the same bond recipe on the same range pressure film. The resulting series of images are shown in Fig. 3, showing a series of adjustments resulting in improved pressure uniformity. Note that after the adjustments, the pressure film analysis shows an offset from the intended recipe pressure of 4 bar, which is a by-product of the instrument assuming a particular wafer area.
In addition to troubleshooting the pressure distribution, the same pressure film data can be used as a tool for monitoring and maintaining performance in manufacturing practices such as six-sigma statistical process monitoring.
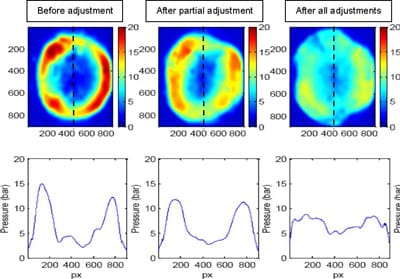
Fig. 3: Bond tool images show improvement to the pressure uniformity as captured by pressure indicating film
2: AU/SN Eutectic Wafer-to-Wafer Bond
Improvements in wafer bond pressure uniformity were applied to a specific project requiring both reliable interwafer electrical connections (~103–104 per wafer), waferto- wafer separation of 2-3 μm, excellent bond gap control, high bond strength and a liquid-proof sealing. Liquid-proof sealing was required for further processing of the bonded stack through metal deposition, lithography and etching steps. Besides these main requirements, the bonding process should not create large stresses that would cause MEMS device performance degradation or reliability issues due to stress relaxation over time. Sources of stress can be the bonding process itself or mismatch of the bonding material thermal expansion coefficients. Preferably, the same process can be used for the bonding of a third wafer to the stack of two bonded wafers.
Au-Sn Solder Wafer-to-Wafer Bond Setup
The type of solder used in our experiments was electroplated Au-Sn solder, aiming for an 80% Au and 20% Sn composition and eutectic temperature of 278°C [2]. Note that the control of the exact solder composition is critical, since a small variation in composition in either direction increases the melting temperature significantly. For example, a +3% shift in composition results in a melting temperature of 340°C, and on the other side a -3% shift results in 333°C melting temperature. Since the solder thickness is comparable to the seed metal thickness, it is also critical to take into account the amount of Au in the seed metal.
The upper and lower wafers bonded in this device are: MEMS wafers containing the micromachined devices with a ring of seed metal around each die, and the CAP wafers containing a corresponding solder ring with underlying seed metal. The solder should wet to both wafers during bonding, thus providing a mechanical bond and a hermetic seal. For initial analysis and test purposes, the silicon MEMS wafers were replaced with glass bond test wafers. SiO2 standoff features in the CAP wafers were included to provide a mechanical stop so that when solder compresses during bonding, the final gap between the substrates is well determined (see figure 4).
Fabrication of the CAP wafers is shown schematically in Fig 4. Standard thickness 6” wafers with TTV smaller than 5 μm were used. After initial oxidation (A), standoffs were defined by oxide patterning. Caps re-oxidation followed (B). Typically, initial oxide thickness was 3.1 μm and 1.0 μm thick oxide was grown at the second oxidation step resulting height of the standoffs of 2.6 μm. Seed metal (4000 A Au) was deposited on the Caps (C) and Au-Sn solder was plated using a photoresist mask (D). Initial plating tests were made using an R&D setup while later work was done using an industrial-grade Cup plater. Plated solder was typically 65% Au and 35% Sn, 2.0-2.5 μm thick, with 5-10% nonuniformity across wafer. Patterning and removal of the seed metal layer from non-plated areas was the last step in the pre-processing of Caps (E).
It was also found that the design of the seed metal pattern has an affect on the bond results [3]. Patterns of several thin solder lines, 50-60 μm wide, provided better sealing than a single, wide solder line of equivalent solder volume. By design, the entire seed layer (4000 A) could be consumed during the bond process to create the eutectic composition. As liquid solder is being compressed during the bonding process, additional Au is being consumed as the solder floods fresh areas of patterned seed layer. Even though the Au diffusion in the solder is fast, the Au concentration at the Fig. 3: bond tool Images show improvement to the pressure uniformity as captured by pressure indicating film periphery of the solder line can be greater than concentration at the centre of the solder line. This difference in composition can make the solder difficult to compress. It was found that several line lines of solder yielded the most consistent results.
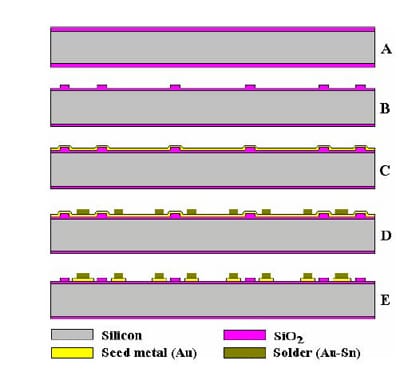
Fig. 4: Fabrication of CAP wafers for bonding tests.
The bonding process was done in a wafer bonder under vacuum with a bond temperature between 300°C and 350°C. The applied pressure was set at 4 bar, and in most cases using the corrected pressure plates from section 1 of this paper. Several types of seed metal were studied, with results summarized in Table 1. For all tests shown here, glass bond test wafers were used instead of the silicon MEMS wafers to allow visual evaluation of solder flow.
Experiment Results on Seed Metallization
For TiW/Au, Ti/Au, and Ti/Mo/Au, the common problem was solder spill-out after de-wetting of the solder from the seed metallization. Figure 5 shows an example of spill-outs in this circumstance. Figure 6 shows a wafer level photograph of spill-outs using TiW/Au. For wafers with dewetting solder, the resulting bond was reasonably strong mechanically (in most cases strong enough to survive dicing) but not liquid proof.
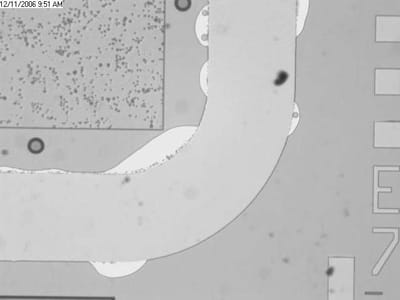
Fig. 5: Example of solder spilled outside of seed metal area after bonding.
The TiW/NiV/Au seed metal is a good example of several difficulties inherent in thin-film solder systems. In this case the solder did not compress or flow due to the presence of Ni in the seed metal. EDX analysis of the solder-seed interface showed Sn depletion, likely caused by a Ni-Sn interaction. With insufficient Sn available to the Au, solder composition is non eutectic and frozen all the way to our maximum temperature of 350 °C. Since the solder was not liquefied, there was minimal solder flow and little or no compression. Surprisingly, the resulting bond still had good mechanical strength.
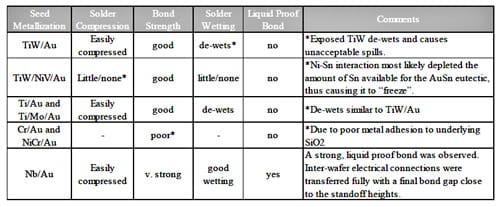
Table 1. Summary of several seed metal bonding results
The best results were achieved with Nb/Au [3,4] seed metallization, where the solder is liquefied, the gap easily compressed to the stops, and solder remains wetted to the seed metal. The final bond strength was good and provided liquid proof sealing of the dies. The final bond gap between the wafers was at the desired standoff height.
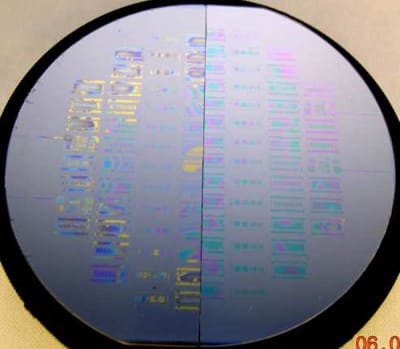
Fig. 6: Left half of wafer (TiW/Au seed) shows an example
of solder spill out after bonding as caused by de-wetting of
solder. Notice that the pressure non-uniformity is evident
by observing that the spill out is most severe on the outer
ring of the wafer and much less towards the center. Right< br /> half of wafer (Nb/Au seed) shows an example of well
bonded wafers with no solder spill outs. The pressure nonuniformity
is not evident on the right side.
A photograph of an example half wafer pair bonded using Nb/Au metallization along side a half wafer pair bonded with TiW/Au metallization is shown in Fig 6. The two samples were bonded separately using the same bond tool and then later broken in half. The de-wetting from the TiW metallization is clearly visible even with the naked eye.
Au-Sn Solder Compression vs Bond Pressure
The amount of solder compression during bonding directly affects the resulting gap between the bonded substrate surfaces. In this part of the study, the applied pressure was varied from 500 mbar to 4000mbar with all else held constant (TiW/Au seed metal was used). The resulting gap was measured at consistent locations across each wafer using a Zygo profilometer and plotted in Fig. 7. At 500 mbar of applied pressure, the measured gaps are widely spread between 4 μm to 6.5 μm. At 1000 mbar, the data set showed a general decrease in final gap, which suggests an increase in solder compression. The range of data here, however, remained relatively high between 3 μm and 5.1 μm. As the bond force is increased further to 2000 mbar, the solder continued to compress with increased pressure. Notice here that the spread of the data tightened due to the gap approaching the standoff height of 2.6 μm. The gap remained the same as pressure increased from 3000 to 4000 mbar, indicating that the physical stop at 2.6 μm has been reached, and that the standoffs are functioning as expected.
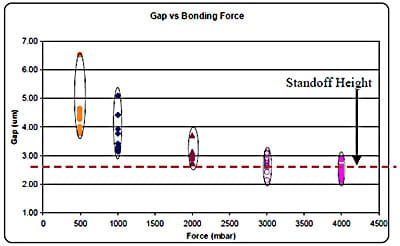
Fig. 7: Measured gap between wafers after bonding. Each colored set of datapoints represent multiple measurements on a single wafer.
3. Summary and Conclusions
Pressure uniformity in a wafer bonding tool can be effectively characterized using pressure sensitive paper and image analysis techniques. The effect of various types of seed metallization in a Au/Sn eutectic wafer bond were studied. For the range of bond parameters and metals studied, Nb/Au produced the best overall results with good mechanical strength, liquid proof seal and no spill-outs. An effective way to produce well defined gaps after bonding was to use SiO2 standoffs.
Acknowledgements
The authors would like to thank Sensor Products Inc. of Madison, NJ, USA for supplying the pressure paper and the detailed analysis support.
Originally distributed at the International Wafer Level Packaging Conference, Santa Clara, California, October 29 – 30, 2009
References
- M. J. Madou, Fundamentals of Microfabrication: the science of miniaturization, Boca Raton, Fla. CRC Press, 2nd edition, 2002
- H. Okamoto, T.B. Massalski (editors), Phase Diagrams of Binary Gold Alloys, ASM International Metals Park, OH, p. 280, 1987
- N. Belov, T-K. Chou, J. Heck, K. Kornelsen, D. Spicer, S. Akhlaghi, M. Wang, T. Zhu, „Thin-Layer Au-Sn Solder Bonding Process for Wafer-Level Packaging, Electrical Interconnections and MEMS Applications”, Proceedings of the International Interconnect Technology Conference, 2009, p. 128
- H. S. Chen, D. D. Bacon, C. H. Chen, G. Kammlott, G. K. Jeng, D. J. Werder, and K. L. Tai, “Simple Nb metal bonding structure,” Applied Physics Letters 66 (17), p. 2191-4 (1995).