
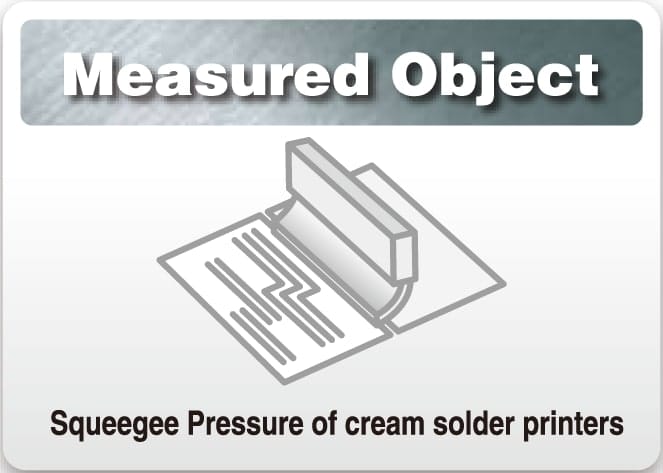
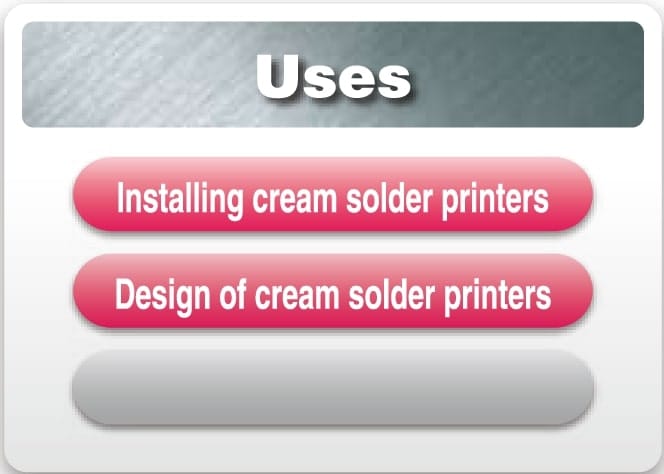
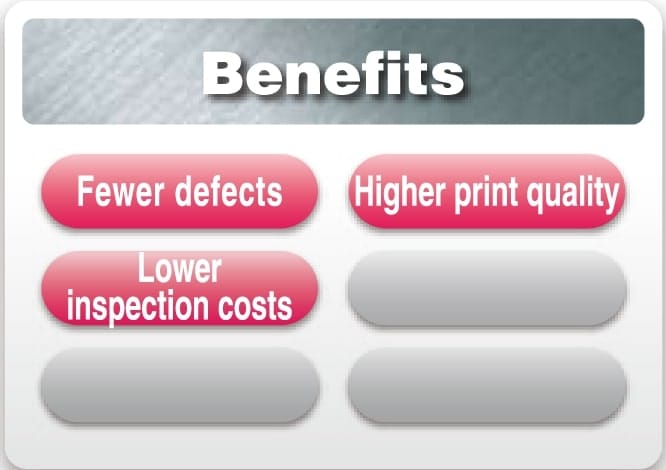
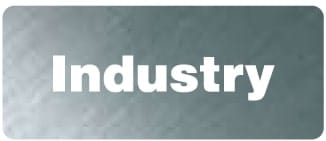
Printed Circuit Board (PCB) electronic component mounting
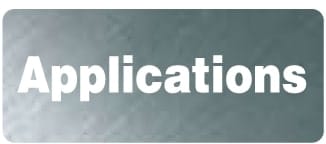
Measurement of squeegee pressure distribution during cream solder printing
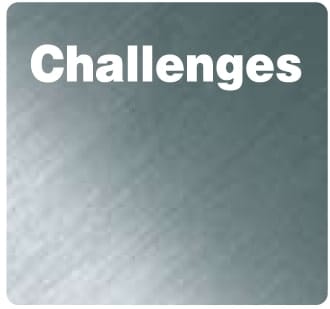
When cream solder is screen printed onto print substrates, any nonuniformity in the squeegee pressure distribution adhesion during subsequent component mounting; and in abnormal conduction when there is excessive solder present.
Despite the importance of squeegee pressure distribution, there was previously no method available to measure it.
Despite the importance of squeegee pressure distribution, there was previously no method available to measure it.
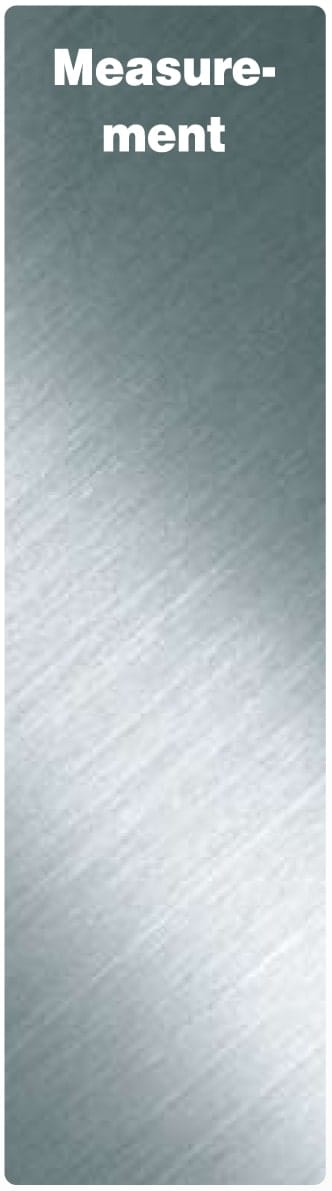
Used product: Prescale (Extremely low pressure 4LW, Ultra low pressure LLLW)
Insert Prescale (4LW, LLLW) between the print substrate and the mask screen, move the squeegee over the mask screen, and then by examining the resulting color of the Prescale, check whether the pressure was uniformly applied.
Check at a glance that the screen and squeegee are set parallel to the print substrate and that the print substrate is not warped or has an uneven thickness.
In the increasingly used process of dual-side mounting, a cushioning support, hollowed out to accommodate the electronic components, is placed at the back of the substrate. If the support is hollowed out for a large number of parts, the pressure at areas where the support is not hollowed out can be significantly higher than that at the hollowed out areas for a given amount of squeegee contact. In this case, in order to ensure uniform application of pressure, it is not sufficient to maintain the squeegee parallel or to adjust the height of the support for uniformilty.
Since Prescale clearly displays the actual pressure between the squeegee and the printer substrate, it cna be used to adjust the squeegee pressure and to develop effective guidelines for installing the support.
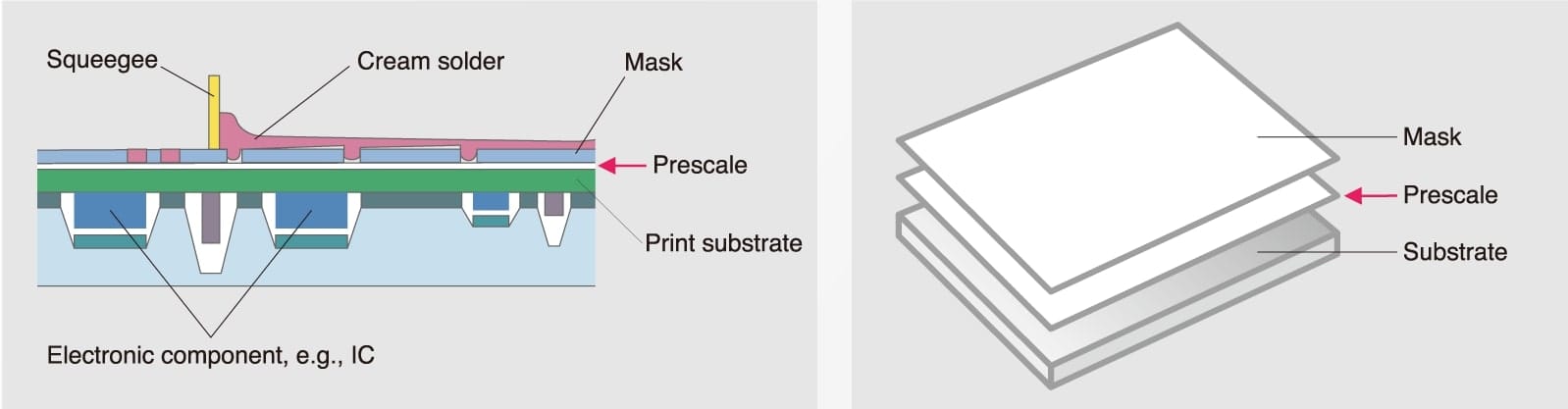
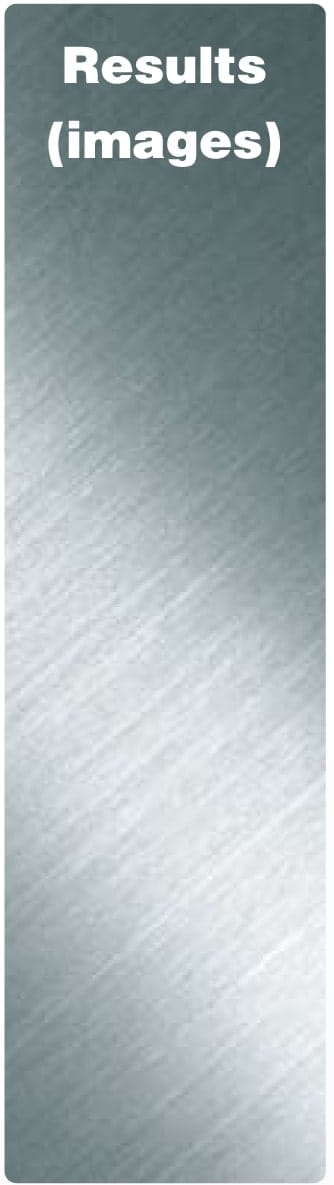
Not good
Squeegee pressure is uneven.
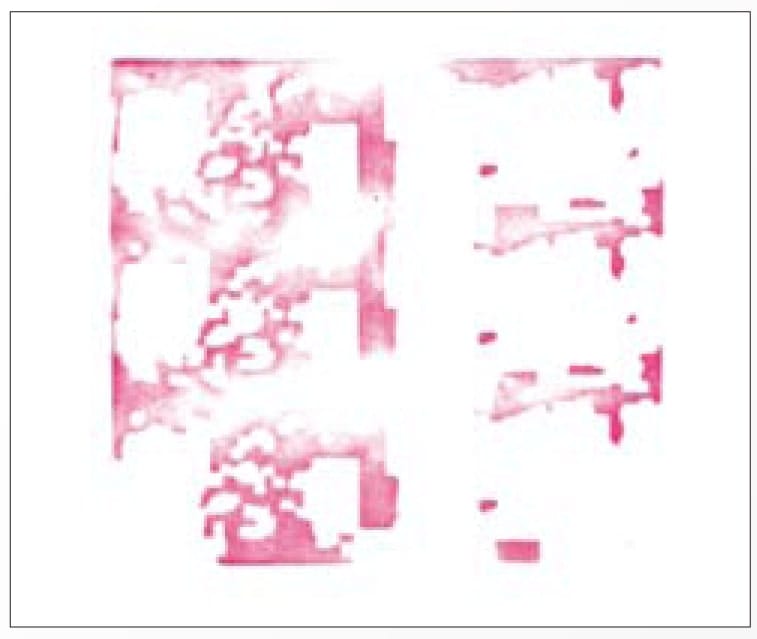
Good
Squeegee pressure is applied evenly.
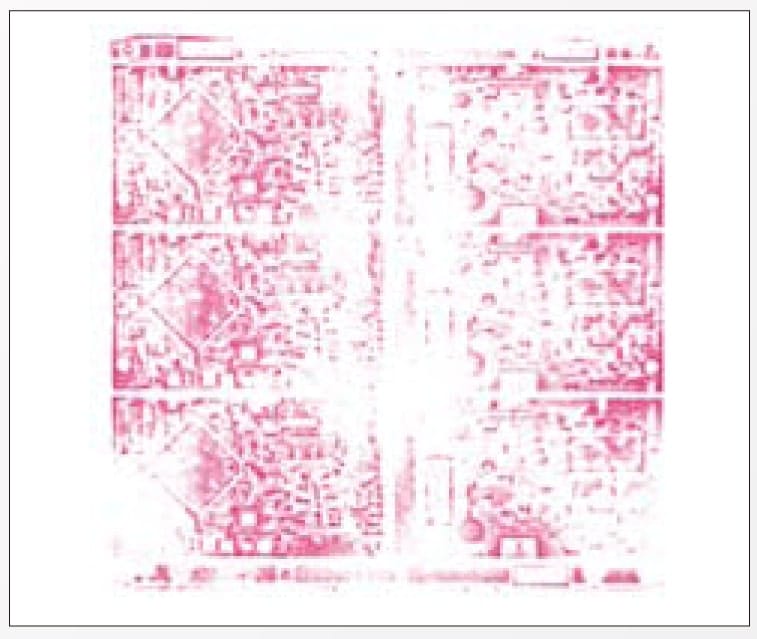
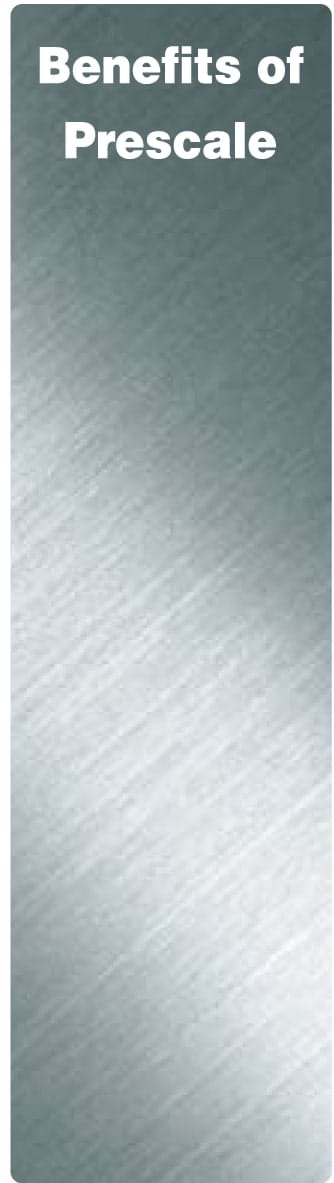
Time savings
Without Prescale, applying cream solder uniformly is a time-consuming, trail-and-error process.
Material savings
Without Prescale, there are substantial losses in components and substrates (since this is a final process).
Quality improvement
Without Prescale, if problems are undetected poor quality products will be shipped.
Without using Prescale
If defects result from component mounting when Prescale is not use d for pressure checking, substantial losses in time/material/quality can occur. There is also a risk of shipping defective products.
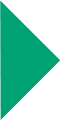
With Prescale
Pressure can be checked when adjusting process conditions, enabling the number of defective prodcuts at the time of final inspection to be greatly reduced. As a result, inspection requires much less effort. Also, since checking can be performed offline designing the support, defects at the manufacturing stage can be dealt with preventively.