Article: Paper, Film & Foil Converter
Pressure is a critical variable in many converting operations. It can be the single factor that determines the success or failure of a flexible packaging laminating adhesive, a heat seal adhesive, or numerous other products. Despite its importance, pressure often receives very scant attention. Converters usually set pressure to a certain predetermined level and vary it when problems occur in an attempt to provide a quick fix. This approach obviously has little scientific merit and is definitely a seat-of-the-pants approach that frequently does not provide optimum results.
Tactile pressure-sensor films are an accurate, efficient, and inexpensive method to determine pressure. These films offer the converting industry a unique opportunity to determine both the distribution and magnitude of most operations where pressure is important. The two most common applications where pressure-sensor films can benefit a user involve monitoring roller contact (nip) pressure and heat sealing jaws. The technology in this product can measure pressure inexpensively and accurately at the interface of any contacting or mating surfaces.
Description of Film
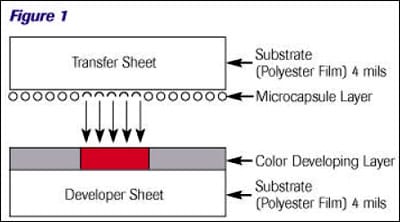
Cross-section view of a pressure-sensor film
The diagram in Figure 1 shows a cross-section view of a pressure-sensor film. The sensor consists of a polyester film contact sheet and a separate polyester film developer sheet. Adhered to the transfer sheet is a microencapsulated layer containing indicator material. Adjacent to this is a color developing layer. Pressure applied to either side of the composite film causes the microencapsulated indicator to rupture and react with the color developing layer. The resultant color relates directly to the magnitude of pressure applied to the film. Higher pressure gives a more intense color. This is very similar to use of pH indicating paper to determine the amount of acidity in an aqueous solution by the color that develops when a drop of the solution contacts the pH indicating paper.
Figure 2 shows color intensity as a function of pressure. During use, visual comparison of color intensity to a color correlation chart provides a pressure-measurement reading that is accurate to ±10%. With the use of optical measuring systems, the pressure reading may be more accurately quantified to ±2%. Use of a pressure-sensor film eliminates the need for expensive and difficult-to-use strain gauges and pressure transducers with accompanying electronic equipment to determine pressure. This ease and accompanying low cost make the product very attractive for the converting industry.
Various films are offered, with some in a range of sensitivities to accommodate varying amounts of pressure. Pressure ranges can start as low as 220 psi (0.14-1.4 Kg/cm²) and go as high as 7,100-18,500 psi (500-1,300 Kg/cm²). Roll and sheet sizes are available with active shelf life varying, but it can be as much as two years. Normal temperature application is 41 °F to 95 °F (5 °C to 35 °C), but some material can withstand much higher temperatures for brief exposures.
Use of Film
Offered in thicknesses from 4 mils to 20 mils, these types of films have found extensive use in industries such as automotive, aerospace, electronics, etc. For these applications and those in the converting industry, a user simply cuts the film to the necessary size to fit into the area where pressure is a concern. After application of the pressure cycle or operation, examination of the color change in the film visually or with an optical instrument provides the value for pressure. Subsequent changes in the pressure and their influence on the properties of the system under examination will readily reveal the effect of pressure on the manufactured product. The thin nature of the film allows it to conform to curved surfaces when necessary. It also is useful for environments that are invasive tolerant or contain difficult-to-access spaces.
Application of force upon the pressure-sensor film ruptures the microencapsulated indicator material causing an immediate and permanent color change. This reveals a high-resolution “image” of pressure variation across the contact area. This indication of pressure distribution is extremely helpful for identification of product variation due to pressure differences from point to point. The product therefore becomes an effective troubleshooting tool in the arsenal of machine operators, process and product control people, technical service personnel, and others in the converting industry.
Typical applications where pressure-sensor film has found use in the converting industry include the following:
- Defects in composition or surface of rollers
- Lack of parallel operation of rollers
- Improper crown correction in rollers
- Inconsistent contact of mating surfaces
- Improper registration of mating surfaces
- Uneven loading by pressure-inducing surface
- Inconsistent web compaction
- Irregularities in sealed areas
- Surface defects in platens.
Typical Applications
Orange peel is a phenomenon in which a flexible packaging adhesive used to laminate two plastic films together becomes distorted to resemble the surface of an orange. A very common cause is excessive coating weight. Sometimes a converter performing this type of lamination can experience low bond levels in the resulting lamination. One solution to increase the bond is to use a higher coating weight. While this does provide a better bond value, at some point the excessive adhesive deposition can cause orange peel. Of equal or greater importance is that the higher application weight of adhesive will increase the raw material costs of the lamination.
Before increasing the adhesive coating weight, the converter should examine other variables, including pressure. Placing a piece of pressure-sensor film onto the nip rollers will enable precise and quick measurement of pressures exerted by the rollers on the laminate material. A pressure-measurement technique such as this easily could reveal the nip roller applied minimal force with a resultant low adhesive bond. One potential explanation for this defect might be that the rubber nip roller had hardened appreciably over time, making it unable to deflect sufficiently to apply correct pressure. Replacing the nip roller would reduce the need to use excessive adhesive. Simple troubleshooting with a piece of pressure-sensor film would be the only step necessary to return the operation to normal tolerances.
Another common application might involve the bonding of heat seal adhesive paper labels to a bottle. Heat seal adhesives require certain levels of time, temperature, and pressure to create a satisfactory seal. Manufacturers of this type of adhesive usually specify a range of values for these variables. Typical heat sealers have settings that allow the operator to select values in the specified ranges. When trouble occurs with low seal values, the operator often will increase one or more variables until the problem disappears. While this procedure may resolve the difficulty, it is at best a “trial and error” approach. Making changes to variables without knowing the cause of a problem is inefficient. All these variables require checking by an operator to ensure they fall within the range specified by the manufacturer. This check should include an independent measurement of each variable rather than simply relying on the gauges of the heat sealing instrument. Pressure-sensor film can indicate quickly whether the pressure of the unit is correct and agrees with the value indicated by the gauge.
A final example concerns sealing a liquid condiment such as lemon juice in a flexible package where the inside sealant layer is polyethylene (PE). Seal packages can develop leaks after storage. What might possibly cause this problem? Although many factors can cause such leaks, application of correct pressure during the sealing operation is one variable that certainly requires investigation. Pressure-sensor film makes this easy. Placing a piece of the indicating film into the sealer will indicate the magnitude of the pressure and the distribution across the package. An indication of uneven distribution of pressure would cause a definite suspicion for the cause of leaking packages, as would an indication of excessively low pressure as Figure 3 shows.
In its use of various adhesive materials on many different types of equipment for varying applications, the converting industry employs pressure to make its products. This can include application of a paper label with a heat seal backing to a bottle for a pharmaceutical product, heat sealing the inner PE layers of a package containing a food item, or nipping an adhesive-coated plastic film to printed paper for subsequent use in a labeling application. An insufficient or excessive amount of pressure or an unequal distribution of pressure between contacting surfaces in all these operations easily can cause product rejection with subsequent expenses and dissatisfied customers.
Pressure-sensor film offers a quick, easy, accurate, and inexpensive method to measure pressure. Using this tactile pressure-measuring film requires only the observation of color change of the material after exposure to pressure. The intensity of color compared with a standard chart or measured with an optical imaging system can provide the magnitude of pressure in a nipping, sealing, or similar operation or the variation of pressure over area in such an operation. Control of pressure in a converting operation by this technique ensures the effects of this important variable do not remain unknown and contribute to product difficulties.